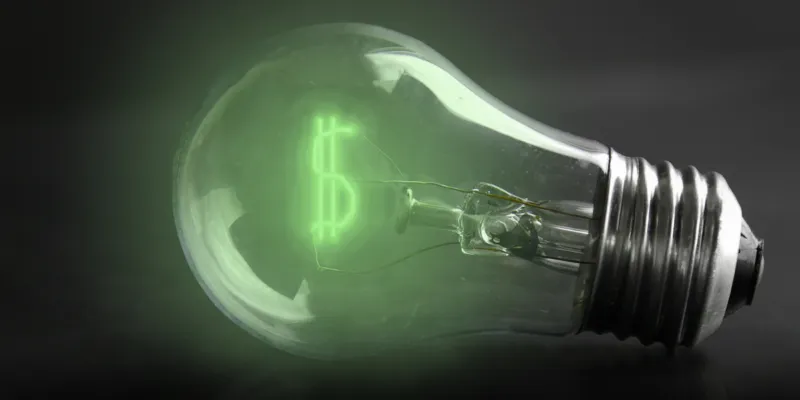
Are Your Energy Costs Unnecessarily High? The 5 Most Common Mistakes
With energy prices continuing to rise, businesses face increasing pressure to reduce operational costs. While it’s natural to focus on improving efficiency, many organisations unknowingly commit simple mistakes that result in unnecessary energy wastage. Addressing these overlooked inefficiencies could lead to significant financial savings, making energy management not just a technical priority but a strategic one. Below, we explore five of the most common mistakes that contribute to high energy costs and how businesses can address them to achieve real results.
1. Leaving Equipment Running During Non-Operational Hours
One of the most pervasive and easily avoidable mistakes is failing to turn off equipment when it’s not in use. Whether it’s lighting, air conditioning, or machinery, leaving equipment running outside of operational hours—overnight, during weekends, or even lunch breaks—can lead to significant energy waste.
Many organisations assume that keeping equipment running constantly, rather than switching it on and off, will prolong its lifespan. However, this belief is largely unfounded for modern machinery. Technological advancements have made most industrial and office equipment robust enough to handle frequent power cycles without damage.
How to Tackle This:
Create a shutdown schedule: Establish clear procedures for switching off machinery, air conditioners, and lighting during non-operational hours. Train staff to follow these protocols, especially during extended breaks and after-hours.
Use automation: Where possible, install automatic timers or sensors to shut down non-essential equipment at the end of the day or when no one is in the room. Automated systems can take human error out of the equation, ensuring consistent energy savings.
By adopting these practices, businesses can see a dramatic reduction in energy consumption without affecting operational efficiency.
2. Believing That Switching Equipment Off Causes Damage
A common misconception in many industries is that switching machinery off for short intervals, such as during breaks or at the end of the day, causes undue wear and tear. This belief leads many to leave equipment running continuously, contributing to high energy bills.
While this might have been true for older, less advanced machinery, it’s not the case for most modern equipment. Advances in technology have made machines more resilient to frequent on-off cycles, especially in industries where equipment is designed for high efficiency and durability.
The Real Cost of Leaving Equipment Running:
Energy waste: Keeping machines on unnecessarily, even for short periods, increases electricity consumption. This is particularly problematic in energy-intensive industries like manufacturing, where every kilowatt-hour counts.
Unnecessary maintenance costs: Constant operation can lead to faster wear and tear on machines, increasing maintenance needs and shortening their lifespan. Turning machines off during idle periods can help reduce these costs.
Businesses can avoid these problems by ensuring that equipment is only turned on when it is actually needed.
3. Using Outdated Machinery That Consumes More Energy
Old and inefficient machinery can be a major contributor to unnecessary energy costs. As machines age, they often become less efficient, consuming more electricity for the same amount of output. This is especially true in industries like manufacturing, where outdated equipment can drive up operational costs significantly.
The Benefits of Upgrading:
Increased efficiency: Newer machines are designed with energy efficiency in mind. For example, in the plastics industry, modern equipment can reduce energy consumption per unit produced by as much as 3% each year. The result is not only a lower electricity bill but also a more sustainable operation.
Reduced maintenance costs: Outdated machinery tends to require more frequent repairs and maintenance, further driving up costs. Investing in energy-efficient equipment reduces both maintenance needs and operational expenses.
How to Assess Whether Your Machinery Needs an Upgrade:
Conduct energy audits: Regular energy audits can identify the efficiency of your current machinery and help you determine whether it’s worth investing in newer equipment. The long-term savings from upgrading often outweigh the upfront costs.
Consider the industry standard: If your competitors are using more energy-efficient machinery, you may be losing your competitive edge. Staying up-to-date with technological advancements ensures that your business remains competitive in an increasingly energy-conscious market.
4. Ignoring Compressed Air Leaks in Industrial Applications
In industrial settings, compressed air systems are often a significant source of energy consumption. However, many businesses fail to properly maintain these systems, resulting in costly air leaks. Leaking compressed air is not just a waste of energy—it also reduces the efficiency of the entire system.
Compressed air leaks can go unnoticed for long periods, and when pressure drops due to these leaks, many businesses react by adding more compressors to compensate. This approach only compounds the problem, leading to even greater energy consumption and higher operational costs.
How to Fix This:
Regular maintenance: Conduct regular inspections to detect and fix leaks in your compressed air system. Simple repairs can prevent energy loss and significantly reduce costs.
Optimise air usage: In many cases, businesses are using more compressed air than necessary. Evaluate how air is being used and consider whether smaller, more efficient compressors can handle the load. This reduces energy consumption without affecting operations.
Addressing compressed air leaks can lead to substantial cost savings, particularly in industries where compressed air systems are essential to daily operations.
5. Failing to Measure and Monitor Energy Use
Perhaps the most significant mistake businesses make is failing to measure and monitor their energy consumption. Without accurate data, it is impossible to identify inefficiencies or understand where energy is being wasted. Data is critical for effective energy management.
The first step to rectifying this mistake is conducting an energy audit. This process involves installing metering systems at key points in your operations to track energy use in real-time. Modern metering systems provide online data that can be accessed from any device, giving businesses the ability to monitor their consumption and make data-driven decisions.
Why Monitoring Matters:
Identifying inefficiencies: Monitoring allows you to pinpoint areas where energy is being wasted, such as machinery left running during idle periods or compressed air systems losing pressure.
Making informed decisions: With accurate data, businesses can adjust operations to reduce energy consumption. For example, shifting production schedules to avoid peak electricity hours can lead to substantial savings, as seen in a milling plant that reduced its energy bill by 11% simply by adjusting production times during winter months.
Ensuring long-term sustainability: Regular monitoring helps businesses maintain energy efficiency over time, ensuring that cost-saving measures continue to deliver results. Without ongoing measurement, initial savings can be lost as operations change or systems become less efficient.
The High Cost of Ignoring Energy Efficiency
The consequences of neglecting energy management go beyond inflated utility bills. Over time, poor energy practices can erode profit margins, weaken a company’s competitive position, and threaten the long-term sustainability of the business. Failure to keep up with energy-efficient practices can result in:
Profit erosion: As energy costs increase, businesses that fail to manage consumption will see their profit margins shrink.
Competitive disadvantage: Companies that neglect energy efficiency may struggle to compete with more efficient, cost-conscious competitors.
Operational risks: Inefficient energy use can strain equipment, leading to more frequent breakdowns and costly downtime.
By addressing these common mistakes, businesses can not only lower their energy costs but also ensure their long-term viability in a competitive market. Energy management is not just a technical necessity—it’s a strategic priority for any business looking to thrive in an increasingly energy-conscious world.